In this tutorial, we’ll guide you step-by-step to design, 3D print, assemble, and program a line-following robot using TCS34725 RGB and KY-033 IR sensors. This robot can autonomously follow a predefined line on a contrasting surface, making it a great hands-on project for learning robotics, sensor integration, and Arduino programming.
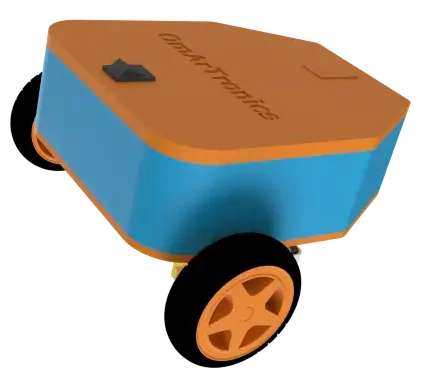
Whether you choose the TCS34725 or KY-033 sensor setup, this project introduces essential skills in 3D design, assembly, and control programming. By the end, you’ll have a functional line-following robot that’s both fun and educational to build!
المكونات المطلوبة:
3D-Printed Parts
- Chassis: Houses the motors, sensors, and Arduino board.
- Sensor Holder: Aligns the sensors for precise line detection.
- Arduino Holder: Mounts the Arduino securely to the chassis.
Motors and Wheels
- 2 DC Motors with Gearboxes: Drive the robot.
- 2 Wheels: Provide mobility.
- 1 Support Wheel: Balances the robot for smooth movement.
Electronics
- أردوينو أونو: Microcontroller for programming and control.
- Arduino Motor Shield Rev3: Drives the motors and distributes power.
- KY-033 Line-Tracking Sensors: Detect the black line using IR.
- TCS34725 RGB Light Sensor: Measures light intensity to differentiate between colors.
Accessories
- Jumper Wires: For connecting components.
- Screws and Inserts: To securely mount parts.
- Battery (e.g., 7.4V LiPo): Powers the robot.
- Power Switch: Optional, for easy on/off control.
Step 1: Designing the Robot in Autodesk Inventor
We started by designing the robot in Autodesk Inventor. The design ensures all components fit securely while maintaining a lightweight and compact structure. Key features include:
- Chassis: A sturdy base for mounting the motors, sensors, and Arduino.
- Sensor Holder: Holds the KY-033 or TCS34725 sensor for precise line detection.
- Arduino Holder: Provides easy access to the Arduino for programming and wiring.
You can download the STL files for these 3D-printed parts from Cults3D.
Step 2: 3D Printing the Components
After finalizing the design, we used a Creality Ender 3 printer to 3D print the components. Materials like PLA or ABS are recommended for durability. Ensure the parts are cleaned and prepared before assembly.
Step 3: Assembling the Robot
1. Mounting the Motors and Wheels
- Secure the motors to the chassis using screws and inserts.
- Attach the wheels to the motor shafts and ensure smooth rotation.
- Mount the support wheel at the rear for balance.
2. Installing the Electronics
- Mount the Arduino Uno and Motor Shield to the chassis.
- Attach the sensors to the sensor holder.
- Connect the Battery and secure all components.
3. Wiring the Components
- Wire the motors to the Motor Shield.
- Connect the sensors to the Arduino pins.
- Ensure the battery is safely connected and add a switch for convenience.
Step 4: Programming the Line Following Robot
KY-033 Sensors Approach
The KY-033 sensors are used to detect the black line on a white surface using IR light. The logic behind the approach is straightforward:
- Left sensor on the line: The robot turns right to adjust back to the path.
- Right sensor on the line: The robot turns left to adjust back to the path.
- Both sensors on the line: The robot moves straight.
- Both sensors off the line: The robot rotates in place to search for the path.
Here’s the complete code for the KY-033 sensors approach:
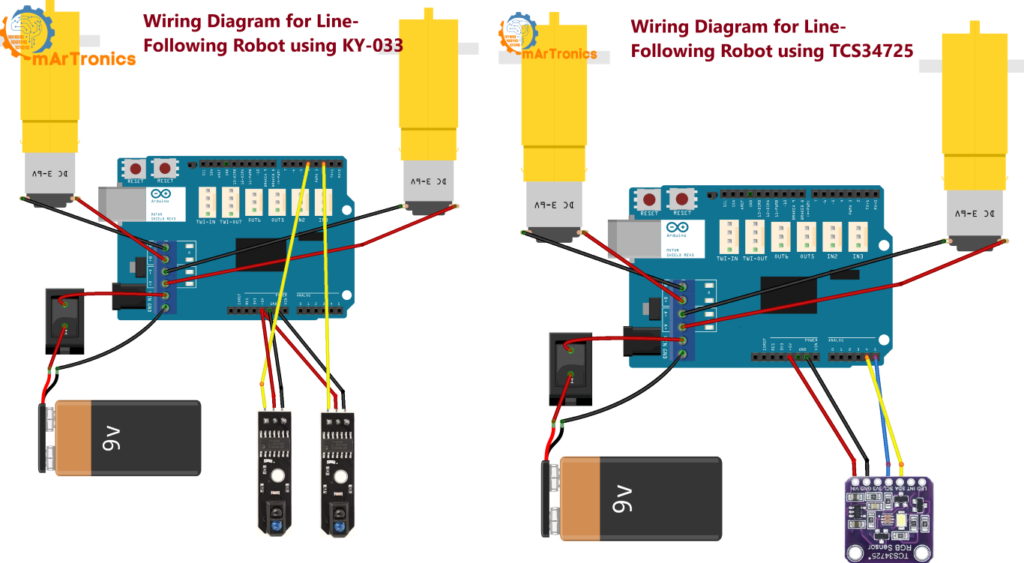
/** * Author: Omar Draidrya * Date: 2024/12/06 * This code controls a Bluetooth robot with an integrated robotic arm. */ // Motor control pins #define DIR_L 12 // Left motor direction #define DIR_R 13 // Right motor direction #define PWM_L 3 // Left motor speed (PWM) #define PWM_R 11 // Right motor speed (PWM) // Sensor pins int sensorLeft = 2; // Left sensor int sensorRight = 4; // Right sensor void setup() { // Configure motor pins as outputs pinMode(DIR_L, OUTPUT); pinMode(DIR_R, OUTPUT); pinMode(PWM_L, OUTPUT); pinMode(PWM_R, OUTPUT); // Configure sensor pins as inputs pinMode(sensorLeft, INPUT); pinMode(sensorRight, INPUT); // Serial communication for debugging Serial.begin(9600); } void loop() { // Read sensor values int left = digitalRead(sensorLeft); int right = digitalRead(sensorRight); // Output sensor data (debugging) Serial.print("Sensor Left: "); Serial.print(left); Serial.print(" | Sensor Right: "); Serial.println(right); // Control logic if (left == 1 && right == 1) { // Drive straight controlMotors(HIGH, HIGH, 105, 105); } else if (left == 1 && right == 0) { // Turn left controlMotors(HIGH, LOW, 105, 85); } else if (left == 0 && right == 1) { // Turn right controlMotors(LOW, HIGH, 85, 105); } else { // Line lost – stop motors // Rotate in place to find the line controlMotors(HIGH, LOW, 70, 70); // Left motor forward, right motor backward // delay(500); // Brief rotation // controlMotors(LOW, LOW, 0, 0); } } // Function to control motors void controlMotors(int directionL, int directionR, int speedL, int speedR) { digitalWrite(DIR_L, directionL); digitalWrite(DIR_R, directionR); analogWrite(PWM_L, speedL); analogWrite(PWM_R, speedR); }
Here’s a detailed breakdown of the code, explaining each section to help you understand how the KY-033 sensor-based line-following robot operates.
1. Motor Control Pins
// Motor control pins #define DIR_L 12 // Left motor direction #define DIR_R 13 // Right motor direction #define PWM_L 3 // Left motor speed (PWM) #define PWM_R 11 // Right motor speed (PWM)
- These pins are used to control the direction and speed of the motors.
DIR_A
andDIR_B
determine the direction of the motors.PWM_A
andPWM_B
control the speed using Pulse Width Modulation (PWM).
2. Sensor Pins
int sensorLeft = 2; // Left sensor int sensorRight = 4; // Right sensor
- The KY-033 sensors are connected to digital pins
2
and4
on the Arduino. - These sensors detect the line by reading either
HIGH (1)
orLOW (0)
.
3. setup() Function
void setup() { // Configure motor pins as outputs pinMode(DIR_L, OUTPUT); pinMode(DIR_R, OUTPUT); pinMode(PWM_L, OUTPUT); pinMode(PWM_R, OUTPUT); // Configure sensor pins as inputs pinMode(sensorLeft, INPUT); pinMode(sensorRight, INPUT); // Serial communication for debugging Serial.begin(9600); }
- Configures the motor control pins as outputs and the sensor pins as inputs.
- Initializes serial communication for debugging purposes.
4. loop() Function
int left = digitalRead(sensorLeft); int right = digitalRead(sensorRight);
- Reads the values from the KY-033 sensors.
1
indicates the sensor detects a line (black surface).0
indicates the sensor does not detect a line (white surface).
5. Debugging Output
Serial.print("Sensor Left: "); Serial.print(left); Serial.print(" | Sensor Right: "); Serial.println(right);
- Prints the sensor readings to the serial monitor for real-time debugging.
6. Control Logic
if (left == 1 && right == 1) { controlMotors(HIGH, HIGH, 105, 105); } else if (left == 1 && right == 0) { controlMotors(HIGH, LOW, 105, 85); } else if (left == 0 && right == 1) { controlMotors(LOW, HIGH, 85, 105); } else { controlMotors(HIGH, LOW, 70, 70); }
- This block controls the robot’s movement based on sensor readings:
- Both sensors detect the line (
1, 1
): Move straight. - Left sensor detects the line, right sensor does not (
1, 0
): Turn left. - Right sensor detects the line, left sensor does not (
0, 1
): Turn right. - Both sensors do not detect the line (
0, 0
): Rotate to search for the line.
- Both sensors detect the line (
7. Motor Control Function
// Function to control motors void controlMotors(int directionL, int directionR, int speedL, int speedR) { digitalWrite(DIR_L, directionL); digitalWrite(DIR_R, directionR); analogWrite(PWM_L, speedL); analogWrite(PWM_R, speedR); }
- This function sets the motor direction and speed using the defined pins.
This implementation ensures accurate line-following behavior using KY-033 sensors. Next, we’ll move on to the TCS34725 sensor approach and explain the corresponding code in a similar manner.
TCS34725 Sensor Approach
The TCS34725 RGB sensor is highly effective for distinguishing the black line from the white background due to its ability to measure light intensity across various wavelengths. This approach includes a calibration phase and uses a PID controller to ensure smooth and accurate path following.
Understanding PID Control Fully in the Context of Line Following
The PID (Proportional-Integral-Derivative) controller is a fundamental concept in control systems, designed to adjust outputs based on feedback from a process variable. In the context of the line-following robot, PID ensures dynamic control of motor speeds, enabling precise and smooth path following.

Components of the PID Controller
Proportional (P) Component
- Purpose: Reacts immediately to the error.
- Equation:
y(t) = Kp * e(t)
- How it works:
The proportional term multiplies the current error (e) by a proportional gain (Kp). This provides a correction that is directly proportional to the deviation from the desired position, such as the center of the line. - Effect:
- Quick responsiveness to errors.
- Larger Kp values result in faster reactions but can cause overshooting or instability.
- Example in Line Following:
If the robot veers off the line, the proportional component immediately adjusts motor speeds to steer it back.
Integral (I) Component
- Purpose: Compensates for accumulated errors over time.
- Equation:
y(t) = Ki * ∫e(t) dt
- How it works:
The integral term sums the error over time and multiplies it by the integral gain (Ki). This helps to correct long-term drift caused by persistent small errors. - Effect:
- Eliminates steady-state error.
- Slower to react compared to the proportional component.
- Example in Line Following:
If the robot consistently drifts to one side, the integral component adjusts the motors to correct the bias over time.
Derivative (D) Component (optional for this project)
- Purpose: Reacts to the rate of change of the error.
- Equation:
y(t) = Kd * (de(t)/dt)
- How it works:
The derivative term predicts future errors based on the rate at which the error changes and multiplies this rate by the derivative gain (Kd). - Effect:
- Reduces oscillations and improves stability.
- Particularly useful for systems experiencing rapid changes.
- Example in Line Following:
If the robot oscillates around the line, the derivative component stabilizes it by reducing abrupt motor speed changes.
Combining P, I, and D in a PID Controller
A PID controller combines these three components to provide precise and stable control. The combined equation is:
y(t) = Kp * e(t) + Ki * ∫e(t) dt + Kd * (de(t)/dt)
How it applies to Line Following:
- The proportional term reacts immediately to how far the robot is from the line.
- The integral term addresses consistent drift over time.
- The derivative term dampens oscillations and stabilizes movement.
Dynamic Error Correction with PID
Error Calculation:
- The error (e) is the difference between the sensor reading and the threshold (middle value).
- This error drives the PID calculations.
Correction Value (y):
- The PID controller calculates y to determine how much to adjust motor speeds:
speedLeft = baseSpeed + y
speedRight = baseSpeed - y
- The PID controller calculates y to determine how much to adjust motor speeds:
Motor Speed Adjustment:
- Motor speeds are adjusted dynamically based on the correction value to maintain the robot on the line.
Advantages of Using PID in Line Following
- Precision: Keeps the robot accurately centered on the line, even in curves.
- Smooth Movements: Avoids jerky or abrupt adjustments by balancing the contributions of P, I, and D.
- Disturbance Rejection: Handles changes in surface reflectivity or motor inconsistencies.
- Adaptability: Can be tuned for different track layouts or robot configurations.
Practical Tuning of PID
Start with Proportional Gain (Kp):
- Gradually increase Kp until the robot begins to follow the line effectively.
- Monitor for overshooting or oscillations.
Add Integral Gain (Ki):
- Introduce Ki to address steady-state errors (e.g., consistent drift).
- Avoid excessive Ki to prevent instability or oscillations.
Adjust Derivative Gain (Kd):
- If necessary, use Kd to stabilize movements and reduce oscillations.
- Avoid setting Kd too high, as it can make the robot sluggish.
Complete Code for TCS34725 Sensor with PID:
/** * Author: Omar Draidrya * Date: 2024/12/06 * This code controls a Bluetooth robot with an integrated robotic arm. */ #include <Wire.h> #include <AFMotor.h> // Initialize TCS34725 sensor Adafruit_TCS34725 tcs = Adafruit_TCS34725(TCS34725_INTEGRATIONTIME_2_4MS, TCS34725_GAIN_4X); // Motor control pins #define DIR_A 12 #define DIR_B 13 #define PWM_A 3 #define PWM_B 11 // PID parameters float Kp = 27.0; // Proportional gain float Ki = 0.5; // Integral gain float Kd = 2.5; // Derivative gain int baseSpeed = 55; // Base speed // Middle value for black/white int middleValue = 3; // Adjusted based on measured values // Global variables for PID float error = 0, previousError = 0, sumError = 0; void setup() { Serial.begin(9600); // Initialize TCS34725 sensor if (!tcs.begin()) { Serial.println("TCS34725 not detected!"); while (1); } Serial.println("TCS34725 detected!"); // Configure pins pinMode(DIR_A, OUTPUT); pinMode(DIR_B, OUTPUT); pinMode(PWM_A, OUTPUT); pinMode(PWM_B, OUTPUT); // Perform calibration calibrateSensor(); } void loop() { uint16_t r, g, b, c; tcs.getRawData(&r, &g, &b, &c); // Calculate error error = (float)c - middleValue; // PID calculation sumError += error; sumError = constrain(sumError, -4, 4); // Limit integral component if (abs(error) < 0.5) { sumError = 0; // Reset for small errors } float differential = error - previousError; float correction = Kp * error + Ki * sumError + Kd * differential; previousError = error; // Adjust speed int speedLeft = baseSpeed + (int)correction; int speedRight = baseSpeed - (int)correction; speedLeft = constrain(speedLeft, 20, 255); speedRight = constrain(speedRight, 20, 255); controlMotors(speedLeft, speedRight); } void calibrateSensor() { uint16_t r, g, b, c; // Measure dark area Serial.println("Measuring dark area..."); controlMotors(-85, 85); // Slightly turn left delay(350); tcs.getRawData(&r, &g, &b, &c); int blackValue = c; Serial.print("Black Value: "); Serial.println(blackValue); // Measure bright area Serial.println("Measuring bright area..."); controlMotors(85, -85); // Slightly turn right delay(700); tcs.getRawData(&r, &g, &b, &c); int whiteValue = c; Serial.print("White Value: "); Serial.println(whiteValue); // Calculate middle value middleValue = (blackValue + whiteValue) / 2; Serial.print("Middle Value: "); Serial.println(middleValue); // Stop motors controlMotors(0, 0); } void controlMotors(int speedLeft, int speedRight) { if (speedLeft >= 0) { digitalWrite(DIR_A, HIGH); } else { digitalWrite(DIR_A, LOW); speedLeft = abs(speedLeft); } if (speedRight >= 0) { digitalWrite(DIR_B, HIGH); } else { digitalWrite(DIR_B, LOW); speedRight = abs(speedRight); } analogWrite(PWM_A, speedLeft); analogWrite(PWM_B, speedRight); }
Here’s a detailed breakdown of the code, explaining each section to understand how the TCS34725 sensor-based line-following robot operates:
1. Sensor Initialization
Adafruit_TCS34725 tcs = Adafruit_TCS34725(TCS34725_INTEGRATIONTIME_2_4MS, TCS34725_GAIN_4X);
- The TCS34725 sensor is initialized with a short integration time and moderate gain to optimize light intensity readings for a line-following application.
2. Motor Control Pins
#define DIR_A 12 #define DIR_B 13 #define PWM_A 3 #define PWM_B 11
- DIR_A and DIR_B: Control the direction of the motors.
- PWM_A and PWM_B: Control the speed of the motors using Pulse Width Modulation (PWM).
3. Calibration Function
void calibrateSensor() { // Measures the light intensity for black and white areas. // Calculates the middle value (threshold) as the average of the two. }
- The robot rotates slightly to measure the black (dark) and white (bright) areas.
- The
middleValue
is calculated and used as the threshold for distinguishing between the black line and the white surface.
4. Main Loop
void loop() { uint16_t r, g, b, c; tcs.getRawData(&r, &g, &b, &c); // Reads the light intensity from the sensor. // Calculates error and adjusts motor speeds using PID control. }
- The light intensity (
c
) is read from the TCS34725 sensor. - PID calculations ensure smooth and accurate adjustments to keep the robot on track.
5. PID Control
float correction = Kp * error + Ki * sumError + Kd * differential;
- Proportional (Kp): Corrects based on the current error.
- Integral (Ki): Accounts for accumulated error over time.
- Derivative (Kd): Predicts and responds to changes in error.
6. Motor Control Function
void controlMotors(int speedLeft, int speedRight) { // Adjusts motor direction and speed based on the calculated correction. }
- Controls the direction and speed of each motor to ensure smooth movement along the line.
Step 5: Testing the Line-Following Robot
To test the functionality of the robot, a 50mm wide white adhesive tape was placed on a dark surface, forming a curvy line. This setup simulates a typical track for a line-following robot. The testing process was conducted using two different sensor configurations:
1. Testing with KY-033 Sensors
- The robot was started directly on the white line with both KY-033 sensors positioned over the tape.
- The robot’s behavior was monitored as it followed the curvy track.
- Adjustments to the code (e.g., motor speed or delay) were made as necessary to ensure smooth and accurate line tracking.
2. Testing with the TCS34725 RGB Sensor
- The robot was placed at the left edge of the white tape, with the TCS34725 sensor positioned near the line.
- The robot performed an automatic calibration by measuring light intensity in two key areas:
- Dark Area: The robot slightly rotated to measure the dark background.
- Bright Area: The robot slightly rotated in the opposite direction to measure the white tape.
- After calculating the middle value as the threshold, the robot began following the line. The PID controller was used to ensure smooth and precise adjustments while navigating curves.